ZM5 Cast Magnesium Alloy: Technical Specifications, Heat Treatment, and Industrial Applications
Magnesium alloys are broadly categorized into two types based on manufacturing processes—wrought magnesium alloys and cast magnesium alloys—though the distinction is not strictly defined. Mg-al alloy is the basis of commonly used Mg alloys. Aluminum exhibits high solubility in magnesium (exceeding 12.7%) with notable solubility variations, resulting in a significant age-hardening effect. By adding other alloying elements to Mg-Al alloys, diverse alloy series can be developed, enabling wide-ranging applications. ZM5, equivalent to the U.S. AZ81 alloy (Mg-8Al-0.5Zn), is the sole domestic Mg-Al-Zn series alloy in China and the most widely applied. Suitable for sand casting and die casting of various components, it offers excellent toughness and high airtightness. The Mg-Al-Zn series alloy (AZ81) can replace cast iron in motorcycle crankcase production, reducing weight by 50 kg and serving as an energy-efficient material.
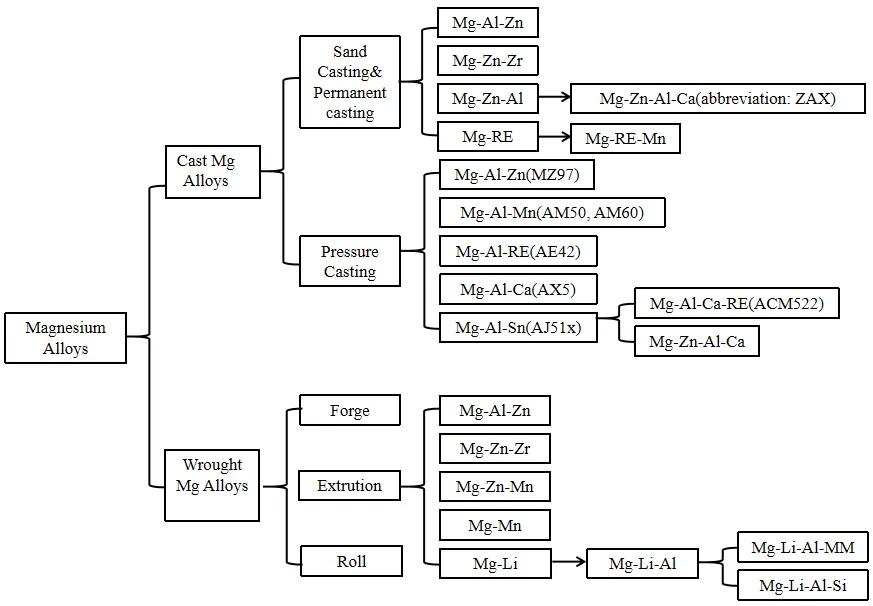
I. Chemical Composition of ZM5 Alloy
The chemical composition and impurity content (mass fraction) of ZM5 alloy are listed below:

II. Heat Treatment and Mechanical Properties of ZM5 Alloy
ZM5 can undergo T4 and T6 treatments. Quenching is performed at 410–420°C with air cooling, followed by aging at 175–200±5°C for 16 or 8 hours. The T6 treatment enhances strength, particularly yield strength, but significantly reduces ductility compared to T4. The heat treatment regimen should align with component requirements. For instance, T6 is preferred for engine parts demanding high structural stability, while T4 is suitable for components prioritizing ductility.
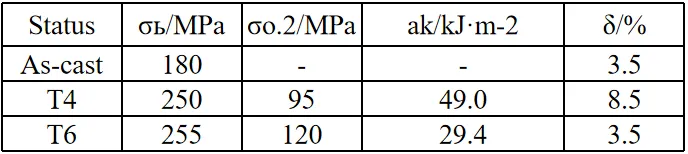
Sand castings and permanent mold castings of ZM5 are typically supplied in T4 or T6 conditions, whereas die castings are used in as-cast (F) state. The alloy can be produced via other casting methods without size restrictions.

Linear expansion coefficient of ZM5 alloy

Resistivity of ZM5 alloy
The ZM5 alloy has high chemical reactivity and its ignition point in air is above 400℃, which is related to the size and shape of the material. When molten magnesium alloy comes into contact with water, it will produce a violent reaction and is relatively dangerous. The corrosion resistance of ZM5 alloy is relatively poor, but by using high-purity magnesium and controlling the content of impurities (especially iron, copper, nickel, silicon, chlorides, etc.), its corrosion resistance can be significantly improved. The following table shows the strength loss of ZM5 alloy after corrosion tests.


Typical high temperature tensile properties of ZM5 alloy castings

Typical high temperature tensile properties of ZM5 alloy castings
III. Applications of ZM5 Alloy
With advancements in high-temperature resistance, cast rare-earth magnesium alloys such as ZM2, ZM3, ZM4, ZM5, and ZM6 are extensively used in manufacturing engine housings, transmission cases.