Mg-RE-Zn-Zr Alloy Properties and Applications
According to alloying principles, Nd among rare earth (RE) elements exhibits relatively high solubility in Mg, contributing significantly to both room-temperature and high-temperature strength. Mixed RE (predominantly Ce) and Ce show the lowest solubility (0.85%), which benefits high-temperature strength but adversely affects room-temperature strength and plasticity. La has the weakest effect, offering inferior contributions to both high- and low-temperature strength compared to Nd and Ce.
ZM3 and ZM4 belong to the Mg-Ce system. Both alloys share identical mixed RE (Ce-rich) and Zr contents (see table below) but differ in Zn content: ZM3 has low Zn (0.2%–0.7%), resulting in lower room-temperature strength, while ZM4 contains higher Zn, enhancing room-temperature strength but reducing high-temperature strength. Both alloys exhibit excellent thermal stability at 200–250°C, with ZM3 maintaining nearly unchanged strength up to 250°C. The as-cast microstructure of Mg-Ce alloys consists of α-phase and RE compounds at grain boundaries. Grain size decreases with increasing dissolved Zr content, improving room-temperature properties. To meet standardized performance requirements, dissolved Zr must be ≥0.4% for ZM3 and ≥0.5% for ZM4 (average grain diameter ≤0.04 mm).
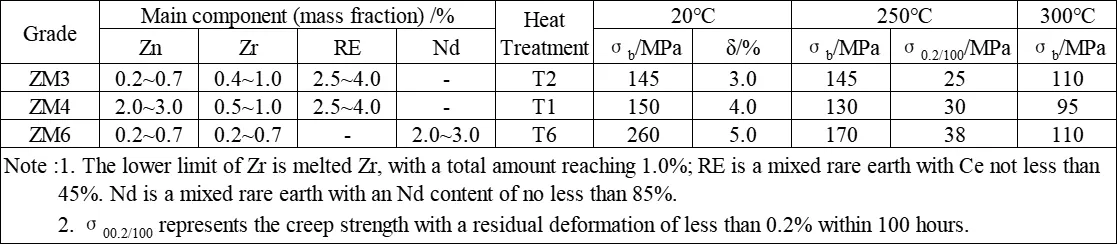
The chemical composition and mechanical properties at high and low temperatures of Mg-RE-Zn-Zr series heat-resistant casting magnesium alloys
I. Chemical Composition and Properties of ZM3 Alloy

Chemical Composition and Impurity Content (wt%) of ZM3
The heat treatment system of ZM3 alloy: ZM3 is typically used in the as-cast state. When annealed, the recommended process is (325±5)°C for 3–5 h, followed by air cooling. The ignition temperature of ZM3 in air is ≥400°C, though flammability depends on part dimensions and geometry. Fine particles or dust ignite readily, while machining chips pose lower fire risks unless heated above ignition points. Thick sections require prolonged heating to combust.
II. Melting and Casting Process of ZM3 Alloy
(1) The alloy is melted in a low-carbon steel crucible for welding. The melting process of zirconium-containing alloys is different from that of aluminum-containing magnesium alloys. It should be carried out in the same crucible as the casting. Transferring to another crucible for casting will cause loss of zirconium content. The alloy is melted under the cover of a flux composed of chlorides and fluorides. During the alloying process, rare earth metals should not be exposed to high temperatures in the air above the liquid surface, and they should not be removed from the liquid surface to avoid oxidation and loss. The loss of zinc can be ignored, while the loss of rare earths varies depending on the casting operation, generally ranging from 10% to 15%. Zirconium is added in the form of a magnesium-zirconium master alloy with a zirconium mass fraction greater than 25%. During refining, a special flux without magnesium chloride is sprinkled on the metal surface. This is because the magnesium chloride in ordinary fluxes will react with rare earth metals to form rare earth chlorides that precipitate from the metal liquid, causing loss of rare earths. Before casting, the metal is left to stand for 15 to 20 minutes to allow the flux to separate from the metal and to precipitate with insoluble compounds. Then, the temperature is reduced to the required level for casting the castings. At least 15% to 20% of the alloy melt should remain at the bottom of the crucible to prevent slag, flux, and insoluble zirconium from being poured into the mold.
(2) During the alloy preparation process, contamination by elements such as aluminum, iron, silicon, and manganese must be prevented, as these elements hinder the grain refinement effect of zirconium.
(3) Due to the low solubility of zirconium and its tendency to form compounds with various impurity elements and be lost, the amount of zirconium added must be 3 to 5 times the required zirconium content in the alloy.
(4) The degree of grain refinement is closely related to the dissolved zirconium content in the alloy. At the same time, the zirconium content has a significant impact on the tensile properties of the alloy. Therefore, melting technology and temperature control are extremely crucial.
III. Physical Properties of ZM3 Alloy
ZM3 alloy is non-magnetic. Its melting temperature range is 590 - 645℃. The thermal conductivity λ is 117 W/cm·℃ at 100 - 300℃. The density γ is 1.80 g/cm³. The resistivity ρ at 20℃ is 73 nΩ·m. The specific heat capacity and linear expansion coefficient of ZM3 alloy are shown in the following table.

The coefficient of linear expansion of ZM3 alloy

The specific heat capacity of ZM3 alloy
The microstructure of ZM3 alloy in as-cast condition consists of Mg solid solution and blocky compounds distributed at the grain boundaries. In cases of deep corrosion, intragranular segregation of Zr can be observed. A higher Zr content leads to finer grain size of the alloy and a lower tendency for compounds to form within dendrites. After annealing at 325°C for 3 to 5 hours, some compounds precipitate as small particles within the grains. ZM3 magnesium alloy has excellent corrosion resistance in dry air, but its chemical stability is poor in moist air, water (especially seawater), and it reacts vigorously with most inorganic acids. In industrial atmospheres, the corrosion resistance of magnesium is similar to that of medium carbon steel. The oxide film of magnesium is not dense, so surface treatment is necessary for long-term use in atmospheric conditions. Magnesium alloys are stable against selenic acid, fluorides, and hydrofluoric acid, forming insoluble salts. Unlike aluminum, magnesium alloys do not react with sodium hydroxide and are also stable in gasoline, kerosene, and lubricating oil. Magnesium is one of the most electronegative metals and should not be directly assembled with parts made of aluminum alloys (except Al-Mg alloys), copper alloys, or steel, as this may cause electrochemical corrosion. Iron, copper, nickel, silicon, chlorides, and other impurities, as well as certain casting defects, can reduce the corrosion stability of magnesium alloys. Zr in the alloy can refine the grain size and eliminate the harmful effects of impurities, significantly enhancing the corrosion resistance of the alloy.
IV. Process Properties of ZM3 Alloy
(1) Forming Performance.
ZM3 alloy has excellent casting processability, with a casting temperature of 720 to 800°C. The alloy has good filling properties, and its fluidity, measured by the length of the cast test bar, is 300 mm. There is no tendency to form microscopic porosity during solidification. The first crack in the thermal cracking tendency test forms at a ring width of 12.5 to 15 mm. The linear shrinkage rate is 1.3%.

Typical tensile properties of ZM3 alloy castings at room temperature and high temperature
(2) Welding performance.
The alloy can be welded by argon arc welding, and has good repair welding performance. Internal stress should be eliminated after welding, and internal quality and surface crack inspection should be carried out after welding.
(3) Heat treatment process
The alloy is only annealed when necessary.
(4) Surface treatment process
The surface of the casting should be chemically oxidized to form a thin protective layer. Before chemical oxidation treatment, the casting must be sandblasted and degreased. According to the different uses of the parts, oil or paint protection should be carried out after oxidation treatment.
(5) Machining and grinding performance
The alloy has excellent machining performance and can be machined at a larger cutting depth and very high speed compared to other metals. The power required to remove a certain amount of metal is lower than that of any other metal. During machining, excellent smooth surfaces can be obtained without grinding or polishing, whether with or without cutting fluid.
V. Applications of ZM3 Alloy
ZM3 alloy is widely used in engine parts, accessories, and various casings.